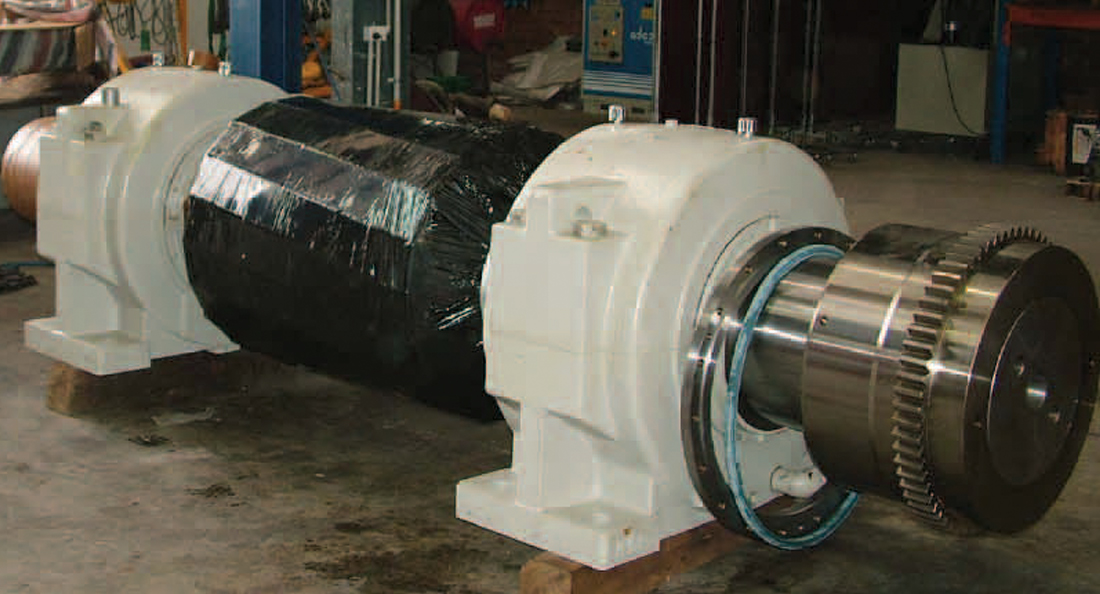
14 Apr Keeping those ball mills turning
When it comes to the mechanical components of ball mills – which are essential to any hard rock mining operation – the focus is often on the trunnion bearings. With diameters typically ranging from one to two metres, these bearings tend to steal the show. But it’s actually the pinion bearings, which are responsible for turning the ball mill around, that work the hardest.
“The pinion drives the trunnion; it’s what makes the ball mill turn. The pinion is a small gear with a matching tooth profile to the ring gear on the ball mill. From a bearing point of view, there are two bearings at the end of the shaft on the pinion and there are two bearings on either end of the ball mill. And obviously, the ball mill bearings are massive in size – which is why they get a lot of attention and are expensive to manufacture,” explains CBC Australia Engineering Manager Anthony O’Keefe. “The pinion bearings are much smaller, but they are heavier duty. Their performance is vital to the whole ball mill operation.”
Due to the criticality of the pinions on a ball mill, most companies will have a spare available. And this is where the expertise of CBC Australia is so important to hard rock mining operators around Australia. The CBC engineering team habitually custom-build pinion assemblies for customers in this segment.
“These companies often rely on our technical support team to assist them with bearing installation on the pinion assemblies,” says O’Keefe. “We recently built a pinion from scratch for a customer in the gold mining industry, who are extremely happy with the result. It’s common for us to assist our customers with pinion assemblies in hard rock mining applications. Whether that is in replacing and installing components, such as the pinion bearings, or setting up a spare pinion that is ready to go in the case of a breakdown.”
O’Keefe highlights, however, that the quality of the bearings and the availability of stock is of key importance. That’s why the partnership between CBC and bearing manufacturer Schaeffler is so crucial.
“Availability of stock is critical. The stock we have on the shelf from Schaeffler is world-leading and our relationship with Schaeffler ensures we have this available to customers,” says O’Keefe. “The German-engineered FAG spherical roller bearing is very high quality and typically seen as the best-suited to this application.”
The FAG spherical roller bearings are part of Schaeffler’s X-life range. According to Schaeffler expert Milos Grujic – Manager of Heavy Industries at Schaeffler’s exclusive ASB Grinding Mills Competence Centre – these spherical roller bearings were the first of their kind and are the best in class.
“The FAG spherical roller bearing has the highest capacity of any spherical bearing that is manufactured. Considering that this spherical roller bearing ‘E’ design was invented by FAG many years ago, suffice to say, Schaeffler is the world leader in the ongoing progression and design of these bearings,” confirms Milos. “These X-life bearings provide up to two times the service life of the old design in this class.”
Milos further explains that the Schaeffler X-life FAG spherical roller bearing is the preferred choice for pinions because it is a low friction, robust bearing with a high axial load-carrying capacity.
“As the pinion gears are driving the girth gear that turns the mill, they need to have a high capacity in order for the gear to have a long life in these conditions,” Milos says. “These girth gears are extremely valuable assets, some of them costing one million dollars or more. So, I cannot stress enough the importance of having a high capacity bearing that can take the high axial loads typical to this application. This will ensure a greater life of the ball mill machinery.”
Moreover, Schaeffler has a special type of packaging, called long-term packaging, which means spare parts such as FAG spherical roller bearings can be kept in storage for many years without deteriorating.
“We can long term (LT) package all of these spares so they can last up to 10 years in warehouses,” says Milos. “They have a colour coding system so that if a product has deteriorated on the shelf, the colour will show that and the package can be returned to Schaeffler who can perform LT repackaging.”
O’Keefe further reiterates how important it is for mining operations to have parts readily available, as ball mills are considered critical assets. CBC’s footprint across Australia and partnership with Schaeffler means that customers have access to critical components such as the FAG spherical roller bearings at all times.
“CBC’s ground cover in the maintenance, repair and operations sector is enormous and combined with Schaeffler’s superior product, we can serve the end user very well,” Milos adds. “Two teams with value-adding products and services are much stronger than one on its own, and they bring immense value to customers.”